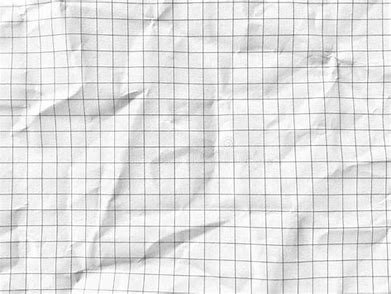
Case Study
Paper Machine Winder
Finished Roll Diameter Increase
Industry: Pulp & Paper
Service Area: Project Mechanical Engineering
Location: Midwest United States
Challenge
The client, a high-volume paper producer, could not produce finished rolls large enough in diameter for their customers’ needs. The client had acquired a used winder that would be large enough, but it would cost about $2 million dollars to refurbish and install. The client requested our services to replace this winder with the used one.
Objective
Provide a solution to produce roll diameters large enough for the customer’s needs of 60” diameter rolls.
Solution
Pillar Engineering LLC worked with the client’s corporate operations team. After reviewing what was being provided from the sister mills to this customer, we realized that the 60” specification was too high and that 57” was large enough. At that point the Pillar Engineering project engineer began a comprehensive audit of the current winder, including:
Mechanical Assessment: What was limiting the machine from producing 57” rolls? Could the drums handle the required weights? Could the rider roll and core chucks raise enough to build these rolls? Were there framework interferences?
Electrical Drive Review: Evaluated the existing motors and drives to see if they were large enough to handle the larger rolls.
Based on our findings, the following improvements were implemented:
New cylinders were purchased to increase the rider roll’s range.
Minor trimming of interference points was made.
Results
Rolls are now produced to the customers specifications
Capital savings of $2-3 million and no extended paper machine downtime
What would have been a $2-3 Million capital project turned into a $20k expense project that was accomplished during two maintenance down days instead of 1 month down for installation.