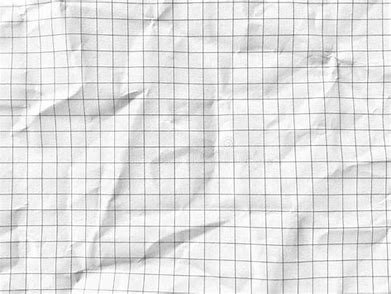
Case Study
Agitator Drive Upgrade
Redesign for Lower Repair Costs
Industry: Pulp & Paper
Service Area: Paper Machine Pulper Agitator
Location: Midwest United States
Challenge
A client had an under machine pulper agitator that had a special motor and belt drive arrangement. The motor failed and needed to be rebuilt.
Objective
Replace the special motor with a standard one that the mill already had for less than the cost of the motor rebuild.
Solution
The Pillar Engineering engineer worked with the mill to determine options for motors that were already in the storeroom stock at the horsepower required. He then determined that a belted arrangement was not going to give the speed needed at the agitator for the standard motor RPMs. At this point, he determined that a standard parallel shaft gearbox with a standard motor would give the RPM and torque that was needed to the agitator. The Pillar Engineering engineer then specified the motor, gearbox, and couplings, along with a rough layout of the new drive pier. The engineer then worked with an in-mill engineer to execute the project.
Results
The complete drive train was replaced for 2/3 of the cost of the special motor rebuild.
The maintenance for the belt drive was eliminated.
A standard motor, already in the storeroom, was used which eliminated the need to purchase a spare.
The overall footprint of the drive was substantially reduced.
The motor was significantly smaller than the previous one, making it much easier for the maintenance crew to replace some day.